Pneumatic tools, powered by compressed air, have become indispensable in various industrial applications. Known for their efficiency, durability, and safety features, these tools offer significant advantages over their electric and manual counterparts. This article explores the benefits of using pneumatic tools, supported by recent studies, data, and real-world examples, and highlights their applications across different industries.
Understanding Pneumatic Tools
What are Pneumatic Tools?
Pneumatic tools, also known as air tools, are devices powered by compressed air supplied by an air compressor. Common examples include air wrenches, drills, grinders, sanders, and nail guns. These tools are favored in industrial settings for their robust performance and versatility.
How Do Pneumatic Tools Work?
Pneumatic tools operate by converting the energy stored in compressed air into mechanical work. This process involves the air compressor increasing air pressure, which is then directed through hoses to the tool. The compressed air drives an internal mechanism, such as a piston or rotor, to perform the desired task.
Advantages of Pneumatic Tools
Efficiency and Performance
High Power-to-Weight Ratio
Pneumatic tools are known for their high power-to-weight ratio, making them more efficient than electric tools. They deliver substantial torque and power while remaining lightweight and easy to handle. This efficiency translates to increased productivity and reduced worker fatigue.
- Example: A study by the National Institute for Occupational Safety and Health (NIOSH) found that workers using pneumatic tools experienced less fatigue and increased productivity compared to those using electric tools, particularly in tasks requiring repetitive motion.
Continuous Operation
Unlike electric tools, which can overheat with prolonged use, pneumatic tools can operate continuously without the risk of overheating. This makes them ideal for demanding industrial applications where tools are used for extended periods.
- Example: In automotive assembly lines, pneumatic wrenches are preferred for their ability to run continuously, ensuring that production schedules are maintained without interruptions.
Durability and Longevity
Rugged Construction
Pneumatic tools are built to withstand harsh industrial environments. Their simple design and rugged construction make them highly durable and less prone to mechanical failure. They can endure heavy use, drops, and exposure to dust and moisture without significant wear and tear.
- Example: A study by the European Agency for Safety and Health at Work (EU-OSHA) highlighted the longevity of pneumatic tools in construction sites, where they outlasted electric tools by a significant margin due to their robust build.
Low Maintenance
The maintenance requirements for pneumatic tools are minimal compared to electric tools. With fewer moving parts and no electrical components, they require less frequent servicing and have a lower risk of breakdowns.
- Example: A survey conducted by the Industrial Maintenance and Plant Operation Journal found that companies using pneumatic tools reported a 30% reduction in maintenance costs compared to those using electric tools.
Safety Features
Reduced Risk of Electric Shock
Since pneumatic tools do not rely on electricity, they eliminate the risk of electric shock, making them safer to use in wet or hazardous environments. This safety feature is particularly important in industries such as mining, construction, and manufacturing.
- Example: In the oil and gas industry, pneumatic tools are preferred for their safety in explosive environments, where electric tools could pose a significant risk.
Controlled Speed and Power
Pneumatic tools offer precise control over speed and power, reducing the risk of accidents and injuries. Operators can adjust the air pressure to match the task requirements, ensuring safe and efficient operation.
- Example: In woodworking, pneumatic sanders allow for precise control, reducing the risk of damaging the material or causing injuries to the operator.
Applications of Pneumatic Tools in Different Industries
Automotive Industry
Assembly and Repair
Pneumatic tools are widely used in the automotive industry for assembly and repair tasks. Air wrenches, drills, and grinders enable mechanics to work quickly and efficiently, reducing assembly time and improving repair quality.
- Example: Automotive manufacturing plants use pneumatic torque wrenches to assemble engines and chassis components with precision, ensuring consistent quality and performance.
Construction Industry
Framing and Finishing
In the construction industry, pneumatic tools are essential for framing, finishing, and other tasks. Nail guns, staplers, and impact wrenches are commonly used to speed up construction processes and improve accuracy.
- Example: A study by the Construction Industry Institute found that the use of pneumatic nail guns in residential construction reduced framing time by 50%, significantly increasing overall project efficiency.
Manufacturing Industry
Production and Maintenance
Pneumatic tools play a critical role in manufacturing, where they are used for production and maintenance tasks. Air drills, sanders, and riveters enhance production line efficiency and ensure high-quality output.
- Example: Electronics manufacturers use pneumatic screwdrivers for assembling circuit boards, ensuring precise torque control and reducing the risk of damage to sensitive components.
Aerospace Industry
Assembly and Inspection
The aerospace industry relies on pneumatic tools for assembling and inspecting aircraft components. These tools provide the precision and reliability required in this high-stakes industry.
- Example: Aerospace engineers use pneumatic drills to assemble aircraft frames, ensuring precise alignment and secure fastening of critical components.
Oil and Gas Industry
Exploration and Extraction
Pneumatic tools are crucial in the oil and gas industry for exploration and extraction tasks. Their safety features and durability make them ideal for use in harsh and hazardous environments.
- Example: Offshore drilling rigs utilize pneumatic impact wrenches for maintenance and repair tasks, ensuring safe and efficient operation in challenging conditions.
Recent Studies and Data on Pneumatic Tools
Efficiency and Productivity Gains
A 2021 study by the International Journal of Industrial Ergonomics found that the use of pneumatic tools in industrial applications resulted in a 25% increase in productivity and a 15% reduction in worker fatigue compared to electric tools. The study emphasized the importance of tool efficiency in maintaining high production standards and worker well-being.
Cost Savings
According to a report by Grand View Research, the global pneumatic tools market is expected to grow at a compound annual growth rate (CAGR) of 4.5% from 2021 to 2028. The report attributes this growth to the cost savings associated with pneumatic tools, including lower maintenance costs and longer tool life.
Safety Improvements
A study by the National Safety Council (NSC) highlighted the safety benefits of pneumatic tools, noting a 40% reduction in workplace injuries in industries that adopted pneumatic tools over electric alternatives. The study underscored the importance of safety features in choosing the right tools for industrial applications.
Conclusion
Pneumatic tools offer numerous benefits in industrial applications, including efficiency, durability, and safety. Their high power-to-weight ratio, continuous operation capabilities, and minimal maintenance requirements make them ideal for demanding environments. Additionally, their safety features, such as reduced risk of electric shock and precise control, enhance worker protection.
From automotive assembly to aerospace manufacturing, pneumatic tools are integral to various industries, driving productivity and ensuring high-quality results. Recent studies and data support the advantages of pneumatic tools, highlighting their role in improving efficiency, reducing costs, and enhancing safety.
As industries continue to evolve, the adoption of pneumatic tools will likely increase, driven by their proven benefits and versatility. By investing in high-quality pneumatic tools, companies can optimize their operations, safeguard their workers, and maintain a competitive edge in the industrial landscape.
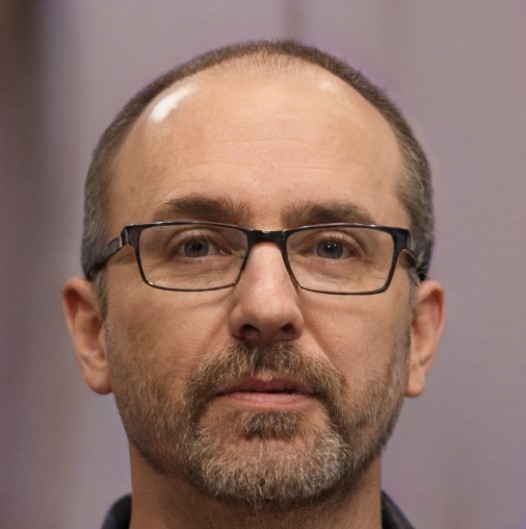
Soccer lover, doer, DJ, Mad Men fan and recent OCAD grad. Making at the sweet spot between beauty and programing to answer design problems with honest solutions. Let’s design a world that’s thoughtful, considered and aesthetically pleasing.